生産性グラフを活用した余力の把握と活用方法について
|
1.職場の実力を見るためには作業間のアイドル時間の把握が重要
|
これまでに製造業における生産性指標の設定方法につき、実践コンサルティングの視点から教科書的な手法ではなく、実態を考慮した現実的な方法(既存データを活用した60点主義でのST設定方法)を説明してきました。また、その中で、生産性の絶対値は必ずしも必要なものではなく、目標設定や異常管理において求められるのはその変化率であることも説明してきました。
では、そのような考え方で設定された標準作業時間(ST)を活用した生産性指標を設定する場合の注意事項につき解説していきたいと思います。ここで重要なのは分母に当たる直接作業時間です。これはモノづくりに費やした作業時間であり、間接作業時間以外の時間となります。
様々な直接作業時間設定をされている会社がありますが、最も多いのが直接作業時間の積み上げ方式によるものです。つまり、あらゆる直接作業の標準作業時間(ST)を設定して、その作業に実際掛った時間を全て記録していくやり方です。これはSTに対しAT (Actual Time)と呼ばれるもので実績時間のことです。この時間がSTより長ければ作業が遅いということになります。
下図(図1)でいうところの左側の考え方です。この事例では本来5hで終了すべき作業(ST)が、実際は6h(AT)掛かったということになり
「労働生産性=掛けるべき時間/掛かった時間=5h/6h×100%=約83%」
ということになります。
|
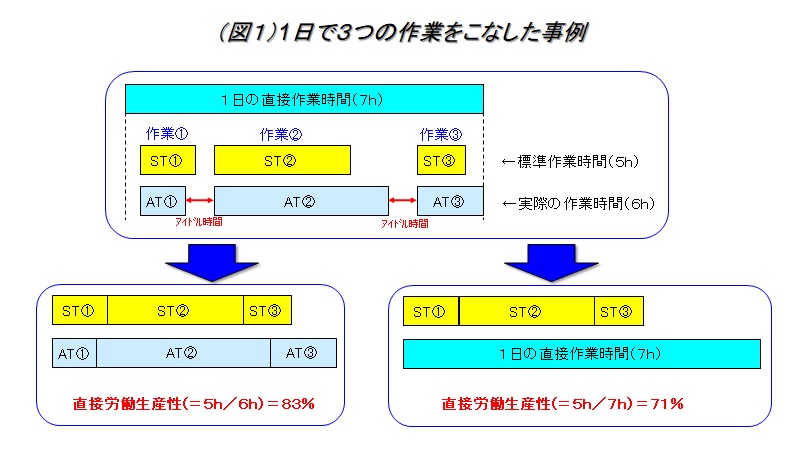
|
果たして、これでこの現場の労働生産性を正確に表していると言えるでしょうか?
一方、上図の右側の考え方もできます。つまり、7hの直接作業時間を与えられ、その時間内に標準時間(ST)5h分の作業しかできなかったということです。この場合では
「労働生産性=掛けるべき時間/掛かった時間=5h/7h×100%=約71%」
となります。
どちらも作業自体は同じ効率なのですが、生産性の見え方に大きな差があります。この2つの生産性は着眼点が異なっていることに気づく必要があります。
左側の生産性はいわゆる作業自体の効率のみを示しており、あるひとつの作業がいかに効率よくできたか?標準時間通りにできたか?を推し量っているもので作業改善の指標となります。作業自体のやり方を変える、治具を活用して効率的な作業にする、新人の教育により習熟が進んでスピードアップした等の改善が進んだことを見える化する指標(作業生産性)と言えます。これはこれで現場ではとても重要な指標ですが、その職場としての効率が向上したかどうかの指標にはなり得ません(作業スピードが上がったのは確かですが)
実は、これ(職場としての効率)を表す指標はもう一方の右側の指標となります。これは7hの直接作業時間を与えられ、その結果として標準時間5h分の作業を終えたということですが、重要なのは作業と作業の間のアイドル時間をも考慮した効率化指標であるということです。いくら、作業自体のスピードを速くしても、その作業を始めるまで、あるいは終わってからだらだらと時間が経過していたとしたら、せっかくの作業スピードアップがムダになってしまいます。つまり、職場の効率化を表す指標としては①作業スピードアップと②作業間のアイドル時間の短縮の2本立てで考えることで初めて、その職場としての効率が見える化されるということです。この指標を先ほどの作業生産性に対して、ここでは職場生産性と呼ぶことにします。
このような仕組みから、会社として、あるいは工場として生産性の向上(職場の効率化)活動をする時の指標として最適なのは後者(職場生産性)であることがお分かりいただけたと思います。経営的な視点で経営者が改善状況を見る場合も、その作業のスピードが上がった、下がったということはどうでもよく、結局何時間かけてどれだけの作業をこなしたのかが関心事項になります。ここには作業スピードだけではなく作業間のアイドル時間も考慮した指標が必要であるということになります。
|
2.作業の実績時間が把握できなくても職場生産性は設定できる
|
既にお気づきのことと思いますが、職場生産性を算出するのに実際に掛った時間(AT)を把握する必要はないということです。この時間の把握が困難であり多大な時間が掛ることから生産性指標の導入に二の足を踏んでおられる会社が多いのが実態であることはとても残念な話です。
一方、この実績時間をIT機器を導入して事細かに採取されている会社もあります。作業者にはそれなりの負荷が掛かっていることになりますが、それで果たして役立つデータが取れているのでしょうか?必ずと言っていいのが、入力が不正確で全実績時間(AT)を足しても1日の作業時間(8h)にならないということが起きています。そもそも1日の全作業をたとえば5分単位で入力せよ、というルール自体がものづくりをミッションとしている現場の作業者にやらせることに無理があることを認識すべきです。結局、入力したデータが信用できないという話になり、せっかく膨大な工数をかけて作業者が入力したデータは使われずに、サーバーに蓄積され続けているというパターンが非常に多いのです。
(この入力を止めることが生産性向上につながるという皮肉な結果を招きます)
前項で話したとおり、職場生産性を算出するには、図1の右側の考え方に従えば良いのです。この職場生産性は
「職場生産性=標準作業時間(掛けるべき時間)/直接作業時間(実際に掛った時間)」
で算出できます。分子はその作業のSTの合計時間、分母は当日の直接作業時間のトータルです。つまり、ひとつひとつの実際に掛った作業時間をとる必要がないことがわかります。この考え方をしっかり持ってほしいと思います。
ここで誤解しないで頂きたのが、ひとつひとつの作業時間の把握が全く必要ないと言っているわけではありません。作業の効率化の結果を把握するためには個々の作業実績時間が必要なのは言うまでもないのですが、1年間ずっと取り続ける必要はなく、改善施策の前後1週間のみ取得する等のスポット的把握で十分であるということです。
以上、まとめますと
① 現場の生産性を把握する場合、作業自体のスピードの把握のみではなく、作業間のアイドル時間を把握する必要がある(=職場生産性の導入が必要)
② この職場生産性の導入に当たっては、個々の作業実績時間を把握する必要はない。(ものづくりのために1日で与えられた直接作業時間さえ明確化すればよい)
これらにより、職場の効率化の見える化指標がかなり身近で手軽に導入できるものであることをご理解いただけたことと思います。まずは実行してみてください。
|
3.職場生産性の活用方法(活動サイクルと余力の把握)
|
前述のように職場生産性を設定し、自職場の直接労働生産性を見える化できたら、これを活用して効率を上げていく必要があります。ここでのポイントは2つあります。
① 日々、改善PDCAを廻す
② 事前に職場の負荷を把握し、余剰工数は直接作業に投入しない
の2点です。これを順に説明していきます。
① 日々、改善PDCAを廻す
当たり前のことですが、生産性指標には活動指標と結果指標の2面性があります。今月の結果を次月の初旬に算出して、目標に対し達成/未達云々といった議論をするために活用する指標は結果指標です。これで目標が未達だったとしても、もはや、前月の結果は覆せないわけですので結果指標となります。多くの会社でこの結果指標的運用(月1回の算出)をされていますが、当月の結果が中旬~下旬に向けて見えてきているにもかかわらず、そこから挽回策を取ることすらできない(見えないのだから)のは大変残念なことです。
やはり1日単位で、昨日の結果を今日見える化して、今日の行動を変えていく運用が必要ではないでしょうか?
② 事前に職場の負荷を把握し、余剰工数は直接作業に投入しない
前述の通り1日単位での見える化をした場合、その延長線上で未来の見える化をすることが可能です。生産計画が見えており明日の計画、1週間先の計画等が見えているのであれば、事前に職場の負荷を把握することができます。
この負荷は「標準作業時間×作業数=掛けるべき時間」としてあらかじめ見えます。これを活用し、自職場の明日の作業工数(掛けるべき時間)が見えれば、保有工数(8h×人員数)に対しどれだけの負荷が必要か?何時間の余力が生まれるのか?が見えるようになります。(下図)
|
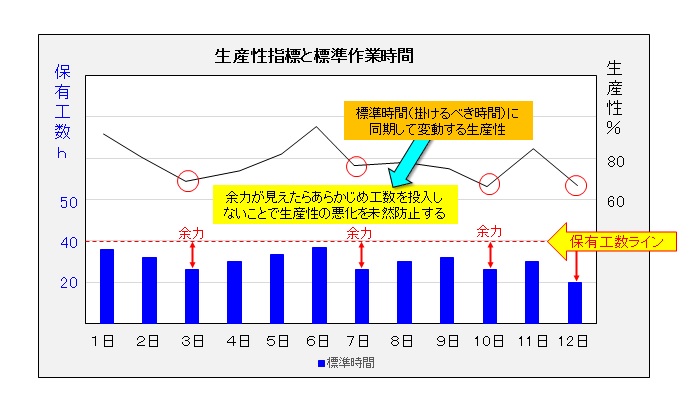
|
これを活用し、事前に投入すべき直接作業時間を決めれば、工数が余剰で間延び作業が発生することを未然防止できます。つまり、毎日、作業密度一定を実現でき、これは生産性が生産数に関係なく一定になるということを示しています。これが、まさに現場管理力ということになるでしょう。多くの会社では生産数が増えると生産性が向上し、生産数が減ると生産性が下がるという現象を繰り返していますが、これは現場管理力がないことを示しています。つまり生産数が減ると、間延び作業や手待ちが横行して効率を下げているということですが、これに気付いていないことになります。
現場管理力がある職場は生産数にばらつきが発生しても常に一定の生産性をはじき出すことが可能となります。やはりこれが製造業の目指すべき姿だと思われます。
以上、製造業の生産性指標の設定と活用方法について、理想論ではなく企業の置かれている現状を踏まえてコンサルタントとしての現実解を解説してきました。この設定方法、活用方法次第で改善活動の効率が大きく左右されることは間違いのないことです。
まずは実践あるのみ、第一歩となる正しい指標の設定から始めてみてください。
|
株式会社アステックコンサルティング
コンサルティング本部 チーフコンサルタント 藤居 隆一
|